The use of ceramics can be traced back to the
early history of mankind. Reliable archaeological research
has shown that the first ceramic figures were formed
from malleable ceramic material and hardened by fire
more than 24,000 years ago. Almost 10,000 years later,
as our ancestors developed settled communities, tiles
were first manufactured in Mesopotamia and India. The
first useful vessels were then produced in Central Europe
between 7,000 and 8,000 years ago.
Until the end of the Middle Ages, the
smelting and process furnaces of the early metal industry
were constructed using natural sandstone bonded with
kaolinite or siliceous material. The development of
synthetic refractory materials (Agricola, Freiberg around
1550) was one of the foundation stones of the industrial
revolution, and created the necessary conditions for
melting metals and glass on an industrial scale, and
for the manufacture of coke, cement and ceramics.
The ceramics industry was an important
partner to the chemical industry. Acid-resistant stoneware
and porcelain were for a long time the most important
materials available for corrosion protection. Nowadays
they have largely been replaced by acid-resistant steels
and enamels, but also by ceramics based on oxides, nitrides
and carbides.
Beginning in the second half of the
19th century, electro-ceramics provided the momentum
for industrial development. During this time, basic
solutions for electrical insulation based on porcelain
were developed.
It is difficult to determine the precise
beginning of modern, high-performance ceramic materials.
Until the turn of the 20th century, the development
of ceramic materials had a primarily empirical character.
Scientific methods were first applied to ceramics in
the course of the 20th century.
The development of manufacturing technologies
using quartz-enriched porcelain achieved bending strengths
of more than 100 MPa for the first time. It was only
in the 1960s, with the systematic development of alumina
porcelain, that marked increases in strength, especially
in large insulators for voltages over 220 kV, resulted
in considerable weight reductions.
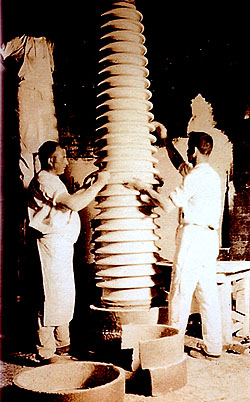
Figure 1: Manufacture
of insulators around 1920.
The growth of broadcast radio in the 1920s led to the
need for special ceramic insulation materials that did
not heat up under the influence of high-frequency electromagnetic
fields. This led to the development of steatite and
forsterite, both of which are still in use today. Research
on oxide magnetic materials began in the 1940s (hard
ferrites, soft ferrites). At this time, capacitor materials
based on titanium oxide were also developed, and research
began on the ferroelectric and piezoelectric properties
of perovskite (BaTiO3). This made a wide palette of
materials available – some even with semiconducting
properties – for sensors, frequency selective
components (filters) and capacitors with high storage
capacity. Theoretical considerations are derived from
basic research by Heisenberg, Dirac, Heitler, Londas,
Hartre and Fock, among others.
A further important milestone was the
introduction of sparkplugs made of sintered alumina
(Siemens, 1929). The development of micro-electronics
increased the demand for aluminium oxide materials,
for example, as a material for substrates and housings.
An important property of this material, in addition
to high electrical resistance, low dielectric losses,
high thermal conductivity, high mechanical strength
and thermal shock resistance, is the vacuum tightness
offered by these new types of material.
While the thermal properties were sufficiently
well explained by the theories of Debye, it was necessary
to develop a theory of fracture mechanics in order to
explain mechanical properties. Whereas initially aluminium
oxide and later zirconium oxide, were first used as
ceramic construction materials, the outstanding properties
of covalently bonded materials based on silicon (silicon
carbide, silicon nitride, SIALONe etc.) were recognised
and exploited at the end of the 1960s. Research into
all these materials continues today. In addition to
the approaches of fracture mechanics, new mathematical
methods and computer simulations have been developed
in order to understand the relationship between microstructure
and properties through modelling. In parallel with the
theoretical developments, process technologies have
been optimised, extending as far as the introduction
of completely new process sequences and sintering methods.
Known materials continue to be improved,
new materials are being developed, and new applications
are being found. The materials of today can no longer
be compared with those that were on the market ten or
twenty years ago. Scientific research is increasing
our understanding of materials. New and improved manufacturing
technologies have brought progress in the areas of quality,
reproducibility and operating safety.
|
|