5.7.6.2 Protection
against abrasion
Ceramic materials are employed in highly
stressed tribological systems because of their resistance
to abrasion. As well as the property of great hardness, this
calls for high stiffness (modulus of elasticity), high pressure
resistance and high fracture resistance. In the case of ceramics,
however, this is at the expense of fracture toughness. Other
positive properties offered by ceramics for use in tribological
systems are their low-density, low thermal expansion, and
their resistance to temperature and to corrosion.
Whereas in the case of adhesion and tribo-chemical
reactions, the wear behaviour is largely dependent on the
chemical and thermo-chemical properties of the wear-protection
material, in the case of abrasion taking place through the
Mechanisms of adhesion and surface spalling, the abrasion
resistance is determined by the physical properties of hardness
and fracture toughness. This is illustrated schematically
in Figure 102.
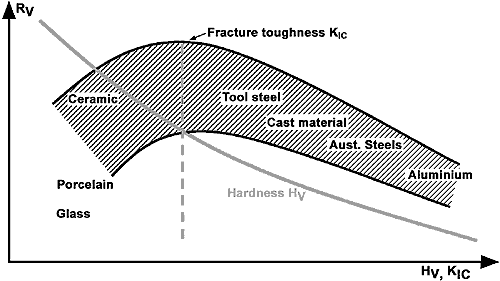
Figure 102: Dependency of the abrasion resistance,
RV, on hardness and fracture toughness
determined in a defined model system
The maximum resistance to abrasion is therefore achieved when
the wear protection material has an optimum combination of
hardness and fracture toughness.
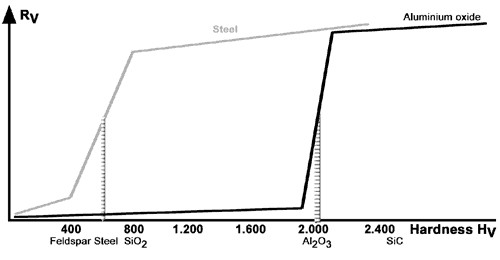
Figure 103: Curve showing abrasion minima
and maxima
When abrasive wear is important, the relationship
between the minimum and maxima of abrasion can be helpful
when selecting the main body. It is based on the familiar
Mohs' hardness scale: a harder material abrades a softer material.
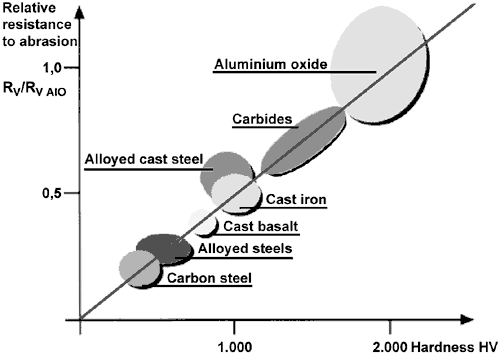
Figure 104: The effect of hardness on abrasion
resistance, RV, with reference
to the abrasion resistance of aluminium oxide, RV AlO
Because of their high hardness levels, abrasion
is of subsidiary importance in the wear of ceramic materials.
Ceramic materials, furthermore, have little tendency to cold
welding that occurs in metals, due to the high lattice bonding
forces (ionic and covalent bonds). Adhesion as an abrasion
mechanism can largely be neglected.
Equally, tribo-chemical reactions occur relatively rarely
when ceramics are used (they always occur, but are relatively
small). In closed tribological systems they cannot be ruled
out, in particular in the presence of solid body and mixed
friction.
In contrast, surface spalling is the main wear mechanism in
brittle ceramic materials in both closed and open tribological
systems.
It is triggered by high stresses from normal forces, or by
high kinetic energy. For example, inclined jet abrasion largely
follows the function WV = ½
mv2 · sin½
where
= angle of incidence. In conveyor systems such as pipe bends,
pipe splits, pipe contractions and nozzles with angles of
up to 30°, aluminium oxide has therefore been found to
be very effective, whereas rubber is optimum at larger angles.
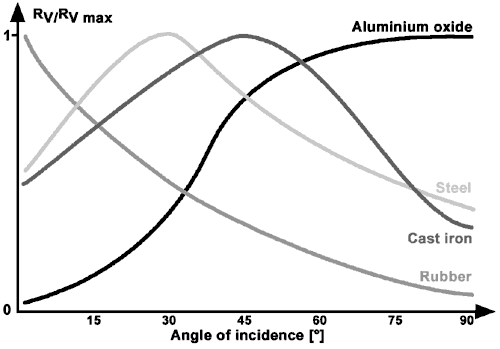
Figure 105: The effect of the angle of incidence
on the abrasion resistance, RV, in
relation to the maximum abrasion resistance
|