4.2.5
Keramische Schichten
Für die Oberflächenveredelung
werden keramische Schichten genutzt, welche an die hervorragenden
Eigenschaften der Keramik, wie hohe Härte und Verschleißbeständigkeit,
elektrische Isolation, niedrige Wärmeleitfähigkeit
und reproduzierbare Oberflächenstrukturen anknüpfen.
Bei der Herstellung keramischer Schichten unterscheidet man
zwischen der Dickschichttechnik und der Dünnschichttechnik.
Dicke Schichten (> 20 µm) werden u. a. durch thermisches
Spritzen aufgetragen. Hier hat sich das Plasmaspritzen hervorragend
bewährt. Beim Plasmaspritzen werden in der ca. 10.000
°C heißen Plasmaflamme oxidkeramische Pulver bzw.
Pulvergemisch wie Aluminiumoxid, Aluminiumoxid/Titandioxid,
Zirkoniumoxid und Chromoxid aufgeschmolzen und auf die vorher
sandgestrahlte Metalloberfläche aufgetragen.
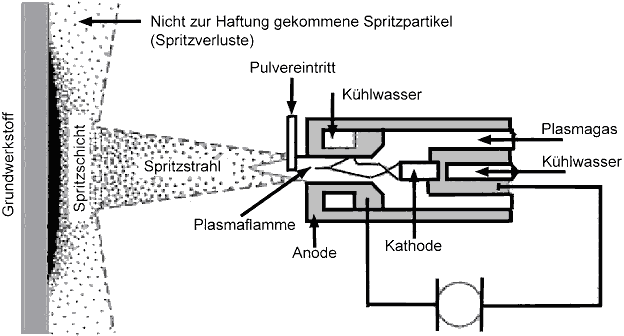
Bild 73: Prinzip des Plasmaspritzens
Vor dem Plasmaspritzen muss jedoch dafür
gesorgt werden, dass durch Sandstrahlen eine zerklüftete
Oberfläche entsteht, in die sich die auftreffenden Keramikpartikel
gut verkrallen können.
Es werden mehrere Einzelschichten aufgetragen, sodass sich
ein lamellarer Schichtaufbau mit einer guten Haftfestigkeit
ergibt.
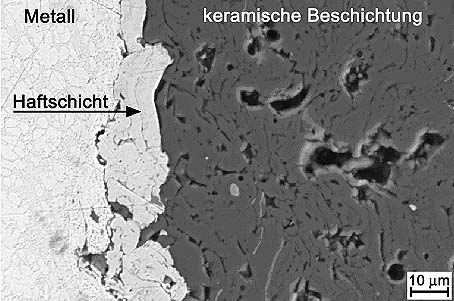
Bild 74: Schliff einer Beschichtung mit Zwischenschicht
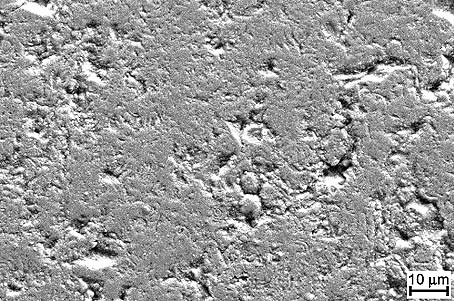
Bild 75: Geschliffene Oberfläche einer
Chromoxidbeschichtung
Vorteil des Verfahrens ist, dass alle metallischen Grundwerkstoffe
(Magnesium ausgenommen) keramikbeschichtet werden können.
Aufgespritzt werden oxidkeramische Pulver wie z. B. reines
weißes Aluminiumoxid für die elektrische Isolation
und als Verschleißschutz, Zirkoniumoxid für die
thermische Isolation. Für den Verschleißschutz
kommen auch Gemische aus Aluminiumoxid und Titandioxid in
verschiedenen Zusammensetzungen zum Einsatz. Titandioxid stabilisiert
die Alpha-Phase von Aluminiumoxid und macht die Keramikschicht
zäh, stoß- und bruchfest. Die Farbe verändert
sich je nach Zusatz von grau über blaugrau bis hin zu
schwarz. Bei Lagern und Pumpen wird Chromoxid wegen seiner
günstigen Reibungseigenschaften gegenüber metallischen
Werkstoffen empfohlen. Eine Zwischenschicht aus Chrom-Nickel
verbessert die Haftfestigkeit.
Die keramische Oberfläche wird durch Nachbearbeitung
auf eine reproduzierbare Oberflächenrauheit eingestellt.
Dabei hat sich bei den meisten Anwendungen die Standardoberfläche
mit Ra = 1,5 bis 2 µm bewährt. Durch Hartbearbeitung
erhält man eine glatte glänzende Oberfläche
mit Ra
0,5 µm.
Die Härte der Keramikschichten liegt für Aluminiumoxid
bei HV
1.800. Zum Vergleich hierzu liegt die Härte von gehärtetem
Stahl bei HV
700 und von hartverchromten Oberflächen bei HV
1.200.
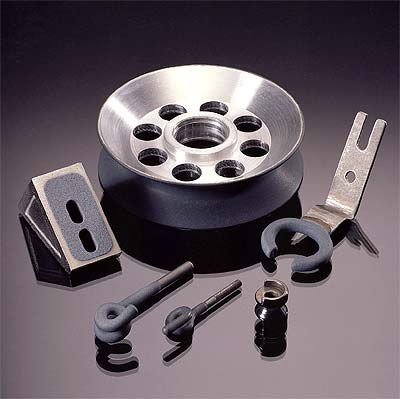
Bild 76: Bauteile mit Beschichtungen für
den Verschleißschutz
Der Vorteil einer 0,1 bis 0,5 mm starken Isolationsschicht
liegt in der Platzeinsparung. Sie ist zudem unempfindlich
gegen Hitze, Schlagbeanspruchung, Licht und bis zu einem gewissen
Grad gegen aggressive Medien und Verschleiß, wobei wegen
der lamellaren porösen Struktur in korrosiver Umgebung
für das Trägermaterial rostfreier Stahl zu empfehlen
ist. Eine wichtige Anwendung der keramischen Beschichtung
ist die elektrische Isolation für Betriebstemperaturen
über 200 °C (bis ca. 500 V), so beispielsweise bei
Heizpatronen. Bis 600 °C ist eine zuverlässige Haftung
der Keramikschicht gewährleistet.
Die Metallteile sollten frei von sichtbaren Lunkern, Riefen
und Löchern sein, da die Keramikschicht die Unregelmäßigkeiten
in der Oberfläche abbildet. Empfohlen wird eine fein
gedrehte oder polierte Metalloberfläche von Rz
8 bis 16 µm. Die Dicke der Metallteile sollte mindestens
1 mm sein, da es sonst zu einem Wärmestau kommt und sich
die Teile verziehen. Dünne Bleche und dünne Drähte
können daher nicht plasmabeschichtet werden. Die maximale
Länge der zu beschichtenden Metallteile ist abhängig
von den Absaugeeinrichtungen und der Peripherie und beträgt
im Allgemeinen 2 m.
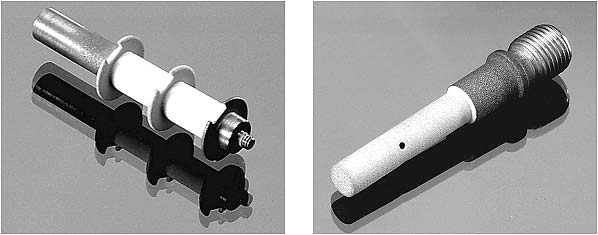
Bild 77 und 78: Bauteile mit Beschichtungen
für elektrische und thermische Isolation
Die Haftfestigkeit auf den Kanten ist eingeschränkt.
Deshalb sollten Kanten mit einem Radius > 0,7 mm verrundet
werden. Zu einer beschichtungsgerechten Konstruktion gehört
die Berücksichtigung des Spannbereichs (Gewinde oder
Stifte). Prinzipiell kann auch partiell beschichtet werden.
Die metallischen Oberflächen werden dann entsprechend
abgedeckt.
Das Beschichtungsverfahren mit Keramik eignet sich sowohl
für Versuchsserien von 1 bis 10 Stück als auch für
Großserien von 10.000 Stück und mehr.
Dieses Verfahren steht für die Möglichkeit, kurzfristig
und schnell zu produzieren. Mit ihm ist es möglich, innerhalb
weniger Tage Metallteile auf CNC-Automaten herzustellen, zu
beschichten und zu bearbeiten.
Interessant sind auch Reparaturbeschichtungen. Verbrauchte
Keramikschichten, die im harten Betriebsalltag Schlägen
und Stößen ausgesetzt wurden, sind einfach abzustrahlen.
Teuere Metallteile können ausgeschliffen und neu keramikbeschichtet
werden.
Gut bewährt haben sich Plasmaspritzschichten z. B. im
Textil- und Drahtmaschinenbau.
Dünnschichten (< 20 µm) werden durch PVD (Physical
Vapour Deposition) oder CVD (Chemical Vapour Deposition),
durch galvanische Verfahren oder durch Sol-Gel-Verfahren erzeugt.
Hier haben sich z. B. bei Werkzeugen die bekannten, goldgelben
TiN-Schichten bewährt.
|