Hierbei werden die Pulverteilchen verdichtet
und in eine zusammenhängende Form gebracht, die für
eine anschließende Handhabung genügend Festigkeit
hat. Je nach Notwendigkeit kann dieses geformte, ungebrannte
Pulverhaufwerk (Grünling oder Grünkörper) vor
dem Brand noch kostengünstig bearbeitet werden, da entsprechende
Arbeitsschritte nach dem Brand sehr viel aufwändiger
sind. Bei den verschiedenen Verfahren der Formgebung muss
darauf geachtet werden, dass es im Grünling nicht zu
merklichen Dichtegradienten und Texturen kommt, weil sich
diese im Brand u. U. noch verstärken, zu Verformungen
führen und innere mechanische Spannungen verursachen
können. Die Auswahl des geeigneten Formgebungsverfahrens
erfolgt meist nach wirtschaftlichen Gesichtspunkten (rationelle
Fertigung).
Die keramischen Formgebungsverfahren lassen sich in folgende
Grundtypen einteilen:
Trockenpressen
wird zur Herstellung von maßgenauen Massenartikeln
eingesetzt. Dabei werden gut rieselfähige Granulate
in Stahlmatrizen verdichtet, die entsprechend dem herzustellenden
Teil profiliert sind. Die hohen Kosten für das Werkzeug
(teilweise aus Hartmetall) sind in der Regel nur bei großen
Serien gerechtfertigt.
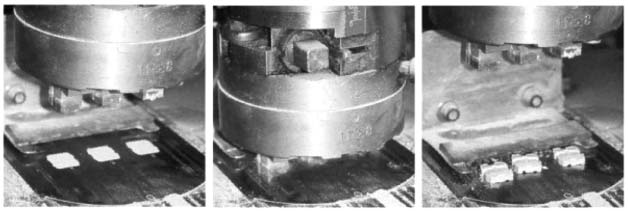
Bild 53: Trockenpressvorgang
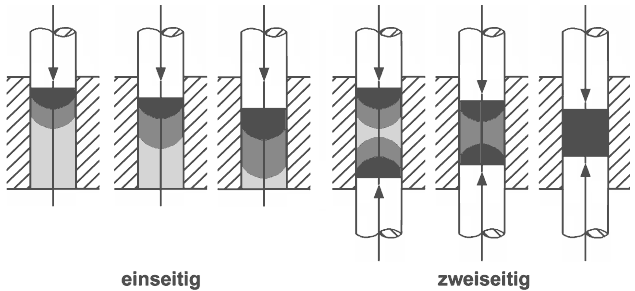
Bild 54: Uniaxiales Trockenpressen, ein-
und zweiseitig, mit Bereichen unterschiedlicher Verdichtung
(Graustufen)
Das Trockenpressen ist bei hohen Stückzahlen
das wirtschaftlichste Verfahren und für einfache bis
komplizierte Geometrien geeignet. Eingepresste Vertiefungen
und Bohrungen sind im Normalfall nur in Pressrichtung vorzusehen.
Je nach Auslegung des Trockenpressautomaten lassen sich
Bauteile von Fliesen- bis zu Streichholzkopfgröße
realisieren. Kleine Scheiben oder Plättchen können
bis zu einer Dicke von ca. 0,8 bis 1 mm gepresst werden.
Für noch dünnere, ebene Bauteile bietet sich eher
das Foliengießverfahren an. Feine Stege o. ä.
im Bauteil lassen sich noch herstellen, wenn das verwendete
Pressgranulat die Hohlräume im Presswerkzeug vernünftig
füllen kann bzw. wenn die Werkzeuggestaltung möglich
ist.
Ab sofort finden Sie hier Videoclips rund um das Thema
Technische Keramik.
Sollten Sie den aktuellen Windows MediaPlayer, RealPlayer
oder QuickTime-Player nicht installiert haben, können
Sie diesen hier kostenlos herunterladen:

Isostatisches Pressen
dient zur Herstellung von gleichmäßig verdichteten
Rohlingen und Großkörpern, die für eine
anschließende spanende Bearbeitung im Grünzustand
geeignet sind. Einfache Gummiformen bedingen zunächst
einfache Rohformen.
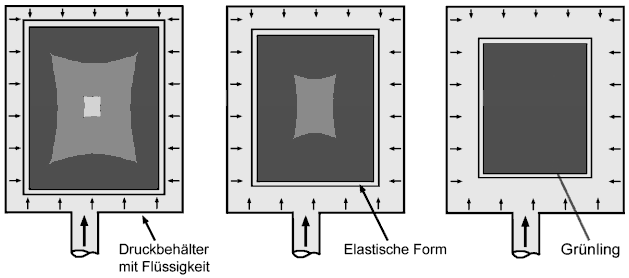
Bild 55: Isostatisches Pressen mit Bereichen
unterschiedlicher Verdichtung (Graustufen)
Diese Formgebung empfiehlt sich für anspruchsvolle
Prototypen- und Kleinserienfertigung, ist aber für
bestimmte Produkte auch voll automatisierbar (Zündkerzen,
Mahlkugeln, kleinere Kolben, Schweißdüsen).
Film: Isostatisches Pressen |
|
|
Ab sofort finden Sie hier Videoclips rund um das Thema
Technische Keramik.
Sollten Sie den aktuellen Windows MediaPlayer, RealPlayer
oder QuickTime-Player nicht installiert haben, können
Sie diesen hier kostenlos herunterladen:

Nasspressen/Feuchtpressen
ermöglicht komplizierte Bauteilgeometrien, z. B. Gewinde,
seitliche Bohrungen, Aussparungen und Hinterschnitte.
Die dazu verwendeten Massen weisen in der Regel Feuchtigkeiten
im Bereich 10 bis 15 % auf. Unter der einachsigen Druckbelastung
werden diese Massen fließfähig, sodass eine relativ
gleichmäßige Verdichtung erreicht werden kann.
Nachteilig wirkt sich aus, dass Nasspressmassen nur begrenzt
Druckspannungen aufnehmen können. Dadurch ist auch
der Verdichtungsgrad begrenzt, der stark vom Feuchtigkeitsgehalt
der Masse abhängt und auch geringer ist als bei Trockenpressteilen.
Darüber hinaus ist u. U. eine Trocknung der Pressteile
vor dem Sintern erforderlich. Hiervon rühren die Mitteltoleranzen
nach DIN 40 680-1.
Extrudieren
erfolgt mittels Kolbenstrang- oder Vakuumschneckenpressen.
Die homogenisierte Masse wird dabei durch ein Mundstück
gepresst und so zu Endlossträngen geformt. Wichtig
ist eine optimale Verdichtung der Masse.
Mit dem Extrudieren lassen sich rotationssymmetrische Teile
wie Achsen oder Rohre besonders gut herstellen. Auch komplizierte
Profile sind bei entsprechender Mundstücksauslegung
machbar. Die herzustellenden Längen der Stränge
hängen im Wesentlichen von der Neigung der Arbeitsmasse
zum Verzug ab.
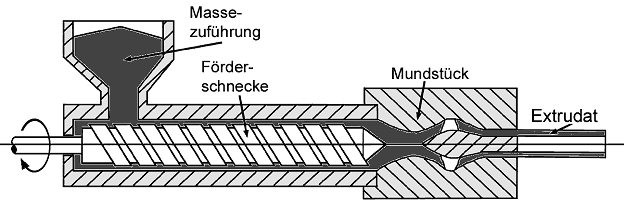
Bild 56: Extrudieren
Spritzgießen
ist für die Massenfertigung komplizierter Teile grundsätzlich
geeignet. Relativ hohe Werkzeugkosten und aufwändige
Entbinderung (Entfernung von organischen Additiven) begrenzen
noch den Einsatz. Die Fördermenge („Schussgewicht“)
beträgt bei den großen Spritzmaschinen typischerweise
bis ? 70 g. Prinzipiell sollten die Wandstärken möglichst
gleichmäßig ausgelegt und nach oben auf ca. 12
mm begrenzt werden.
Schlickergießen
ist eine einfache Methode für die Herstellung von Prototypen
und geometrisch komplizierten Bauteilen, aber auch von relativ
großen Körpern. Dabei können dünne
Wände, aber auch Vollkörper realisiert werden.
Beim keramischen Schlickerguss wird eine stabile Suspension,
der so genannte Schlicker, in eine poröse, saugfähige
Gipsform gegossen. Durch den Entzug der Suspensionsflüssigkeit
bildet sich an der Formenwand eine Teilchenschicht, die
beim Vollguss bis zum fertigen Formkörper anwächst.
Beim Hohlguss wird der überflüssige Schlicker
beim Erreichen der gewünschten Wandstärke ausgegossen.
Foliengießen
Hierbei wird ein keramischer Schlicker mit verschiedenen
organischen Zusätzen auf ein endloses, über Rollen
angetriebenes Stahlband gegossen. Das heißt, der Schlicker
läuft kontinuierlich aus einem Vorratsbehälter
durch einen einstellbaren Spalt auf das Band. Im Gegenstrom
wird zur Trocknung Warmluft über die Folie geblasen,
sodass man am Bandende eine, wegen der organischen Zusätze
flexible Grünfolie erhält. Diese kann entweder
aufgewickelt und für die spätere Weiterverarbeitung
eingelagert oder direkt durch Schneiden, Stanzen, Prägen
o. ä. weiterverarbeitet werden.
Mittels Foliengießen lassen sich typisch keramische
Teile mit einer Dicke im Bereich 0,25 bis 1,0 mm herstellen.
Die Formteile eignen sich zur Herstellung von Substraten,
Gehäusen, Kondensatoren und Multilayeraktoren.
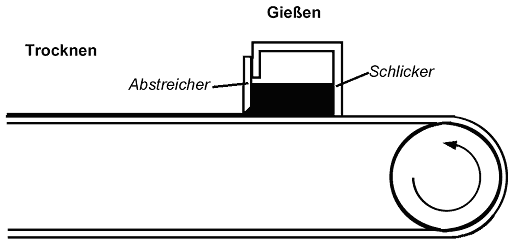
Bild 57: Foliengießen
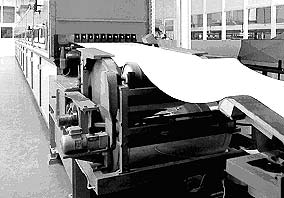
Bild 58: Foliengießmaschine
Ab sofort finden Sie hier Videoclips rund um das Thema
Technische Keramik.
Sollten Sie den aktuellen Windows MediaPlayer, RealPlayer
oder QuickTime-Player nicht installiert haben, können
Sie diesen hier kostenlos herunterladen:

Die Auswahl
des jeweils anzuwendenden Formgebungsverfahren wird aus
technischer Sicht durch die Geometrie und Größe
der Bauteile und die an sie gestellten Anforderungen bestimmt.
Stückzahl, Rohstoffeinsatz und Prozesskosten entscheiden
über die wirtschaftlichste Lösung.
Die hier zunächst vorgestellten Formgebungsverfahren
können noch durch weitere ergänzt werden.
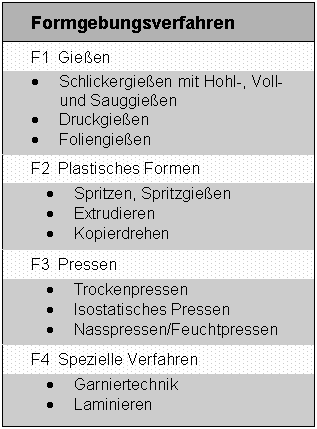
Tabelle 3: Auswahl keramischer
Formgebungsverfahren in der Zusammenstellung
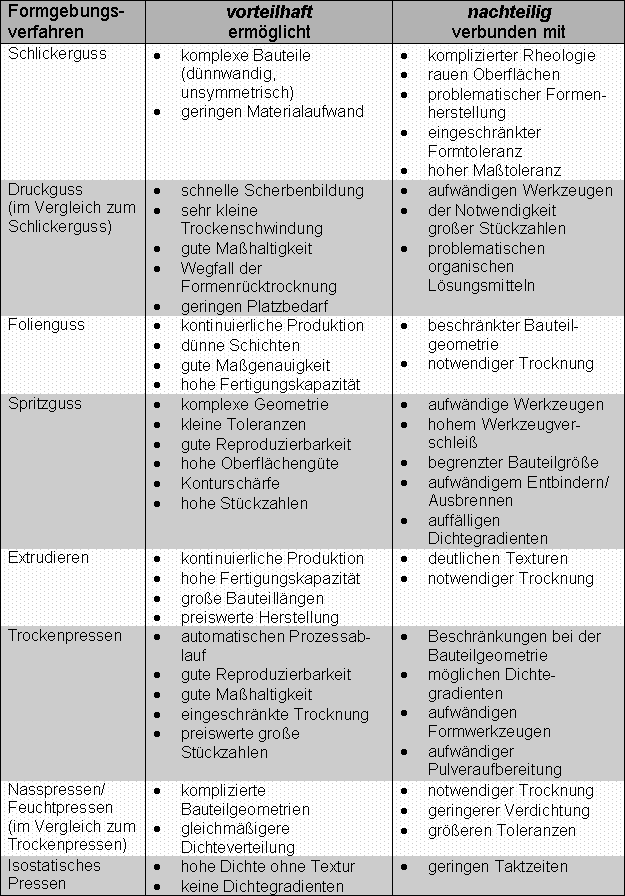
Tabelle 4: Vor- und Nachteile üblicher
Formgebungsverfahren