4.1.5 Abmessungen
und Schwindung
Ziel der Formgebung des Grünlings aus
keramischer Masse ist es, dass später Abmessungen und
Form des herzustellenden gebrannten, keramischen Werkstückes
möglichst genau und vollständig erreicht werden,
da jegliche Nachbearbeitung gebrannter Keramik wegen ihrer
außerordentlichen Härte aufwändig ist.
Im Gegensatz zu Metallen erfolgt die Formgebung der Keramik
nicht als letzter Schritt in der Verfahrenskette, sondern
nahezu am Anfang.
Die ungebrannten Rohlinge (Grünlinge) für die keramischen
Bauteile müssen in der Regel größer geformt
werden als der verlangte fertige Artikel, da als Besonderheit
der keramischen Technologie in der Prozessfolge bei fast allen
Werkstoffen eine Volumenverkleinerung der Bauteile auftritt.
Diese beruht auf den Volumenabnahmen bei Verfahrensschritten
wie, z. B. Entwässerung, Trocknung und Brand.
Erst im Sinterbrand bildet sich der eigentliche keramische
Werkstoff mit seinem charakteristischen Gefüge, und aus
dem Rohstoffgemisch wird der Werkstoff.
Die hohen Temperaturen führen zu einer Abnahme der spezifischen
freien Oberfläche der Partikel (Diffusionsvorgänge,
Bildung von Schmelzen, Phasenumwandlungen) und damit zu einer
Verdichtung des Gefüges, mit der eine Verminderung des
Volumens einhergeht, die als Schwindung bezeichnet
wird. Formgebungswerkzeuge müssen deshalb mit einem „Aufmaß“
gegenüber der gewünschten Bauteilgeometrie ausgelegt
werden, das die in den folgenden Verfahrens-schritten eintretende
Bauteilschwindung kompensiert.
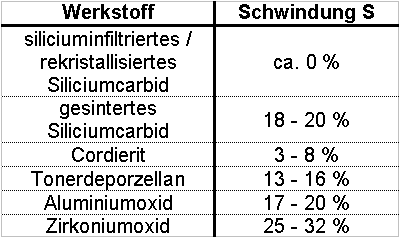
Tabelle 6: Längenschwindung einiger
Werkstoffe
Bereits geringste Schüttdichteschwankungen
der Pressgranulate führen beim dosierten Füllen
der Pressform dazu, dass die Rohlinge unterschiedlich stark
verdichtet werden und damit beim Sintern maßlich verschieden
schwinden.
Die Längentoleranzen der Sinterkörper liegen daher
bei Standardverfahren trotz Dichtestreuung und großer
Schwindung beim Sintern bei ca. ? 2 %. Diese Standardtoleranzen
sind in DIN 40 680 festgelegt. Durch den Einsatz von optimierten
synthetischen Pulvern oder Arbeitsmassen und durch ausgefeilte
Prozessführung lassen sich heute auch Toleranzen von
< ? 0,5 % garantieren.
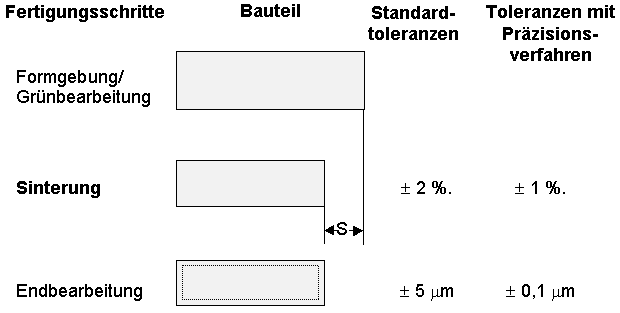
Bild 61: Maßtoleranzen
nach dem Sintern und nach der Hartbearbeitung
Alle Maße sollten, anders als bei
metallischen Werkstoffen üblich, möglichst mit größeren
Toleranzfeldern zu versehen, um erhöhten Fertigungsaufwand
zu vermeiden. Es muss vor allem großer Wert darauf gelegt
werden, dass der Anwender engere Toleranzen auf die absolut
notwendigen Funktionsmaße des keramischen Bauteils begrenzt.
|
|