4.1.4 Vom Formen
zum Sintern
Die nach den urformenden Verfahren Gießen,
plastisches Formen und Pressen hergestellten Grünlinge
enthalten neben den keramischen Pulvermischungen (einschließlich
der permanenten Additive) in der Regel noch Feuchte und meist
organische Verflüssigungs-, Plastifizierungs- und Bindemittel
oder andere Hilfsstoffe.
Alle bei hohen Temperaturen flüchtigen, also verdampfenden
oder verbrennenden Anteile müssen vor dem Brennen aus
dem keramischen Grünling entfernt werden, was besondere
Sorgfalt erfordert, damit sie ihn ohne Schädigung verlassen
können.
Abhängig vom Pulver, von der Bauteilform und größe
sowie von der gewählten Urformgebung weist der Grünling
mehr oder weniger große Dichtegradienten auf, die sich
nach dem Brennen u. U. auch noch im Toleranzspiel der Bauteile
bemerkbar machen können.
Trocknen
In einer geformten feuchten Masse sind alle Teilchen mit einer
Wasserhülle umgeben. Mit der Abgabe des Wassers rücken
die Teilchen einander näher, und es findet eine Volumenabnahme
statt, die so genannte Trockenschwindung.
Die Trockenschwindung nimmt mit der Höhe des Feuchtegehalts
zu. Sie ist außerdem von der Korngröße, der
Art der Rohstoffe und vom Formgebungsverfahren abhängig.
Z. B. ist durch die plättchenförmige Gestalt der
Tonmineralteilchen bei stranggepressten Körpern aus Porzellan
die Schwindung längs des Stranges geringer als senkrecht
dazu. Solchen Orientierungen oder so genannten Texturen muss
man nach Größe und Geometrie der keramischen Bauteile
mit vorsichtigem Trocknen Rechnung tragen.
Beim Trocken kommen unterschiedliche Verfahren zum Einsatz,
die den jeweiligen keramischen Bauteilen angepasst sind.
Ausbrennen
Grünkörper aus natürlichen plastischen Massen
haben oft eine ausreichende Rohbruchfestigkeit. Diese kann
jedoch mit organischen Additiven verbessert werden. Solche
Zusätze sind darüber hinaus bei von Haus aus unplastischen
Massen unverzichtbar.
Das Ausbrennen solcher restlichen Plastifizierungs- und Verfestigungsmittel
und anderer organischer Additive bedarf eines sorgfältig
angepassten Temperatur-Druck-Atmosphären-Zeitprofils,
um ein schädigungsfreies und reproduzierbares Austreiben
der Hilfsstoffe aus dem feinporösen Formkörper sicher
zu ermöglichen.
Eine Variante des Ausbrennens ist das so genannte Verkoken,
z. B. bei SiC. Dabei werden u. a. Kunststoffanteile in Kohlenstoff
umgewandelt, der im Gefüge verbleibt und sich im folgenden
Reaktionsbrand mit Hilfe von zugeführten Reaktionsstoffen
zu einer keramischen Matrix umsetzt.
Nach dem Trocknen und Ausbrennen bzw. Verkoken wird das Gefüge
des Grünlings (Pulverhaufwerk in Bauteilform) lediglich
durch Adhäsionskräfte zusammengehalten und bedarf
einer besonders sorgfältigen Handhabung während
der weiteren Prozessschritte. Aus diesem Grund werden Trocknen
und Ausbrennen nach Möglichkeit mit dem keramischen Brand
zusammengefasst.
Verglühen
Um das Handhabungsrisiko zu reduzieren und die Alternative
der Weißbearbeitung zu ermöglichen, kann der Formkörper
im Vorbrand durch Verglühen mit relativ geringer Schwindungsrate
vorverfestigt werden. Dazu müssen Festigkeit und Schwindungsrate
über die Prozessparameter reproduzierbar eingestellt
werden.
Brennen
Das Ziel der keramischen Technologie ist die Herstellung eines
mechanisch festen Körpers, der unterschiedlichsten Anforderungen
und Belastungen beim Anwender standhält. Zwischen den
einzelnen Teilchen des Grünlings besteht nur geringe
Haftung. Die keramische Bindung und damit die hohe Festigkeit
erhält man erst durch das Brennen bei hohen Temperaturen.
Der Brand ermöglicht das Sintern (mit flüssiger
Phase oder auch ohne) und lässt somit erst den eigentlichen
keramischen Werkstoff entstehen.
Die Vorgänge beim Sintern keramischer Körper sind
sehr komplex (Mehrstoffsysteme) und laufen je nach Reinheit,
Korngröße, Packungsdichte und Brennatmosphäre
unterschiedlich schnell ab. Oxidkeramische Produkte mit hohem
Reinheitsgrad sintern durch Festkörperreaktion und benötigen
dabei viel höhere Sintertemperaturen als feldspathaltige
Massen, wie z. B. das Porzellan mit einem hohen Anteil an
Schmelzphase.
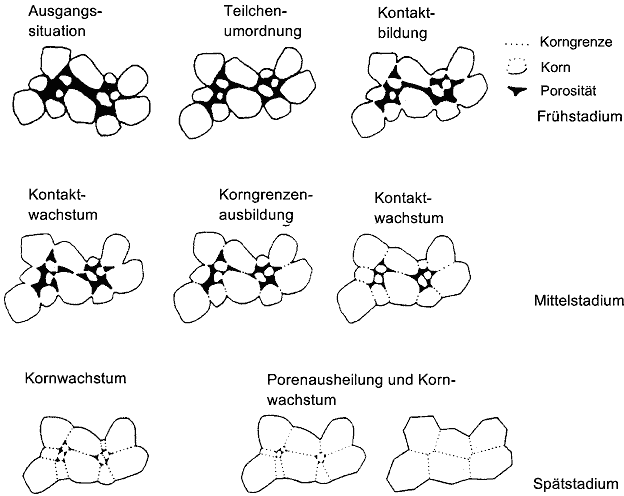
Bild 59: Kornwachstum während des Sinterprozesses
Durch die Vorgänge beim Brand findet
eine Verfestigung und Verdichtung der Produkte statt, die
sich auch in einer Abnahme der Porosität äußert.
Dieser Prozess bewirkt insgesamt eine Volumenabnahme, die
so genannte Brennschwindung. Diese kann für verschiedene
keramische Werkstoffe sehr unterschiedlich sein.
Ähnlich wie beim Trocknen benötigen keramische Produkte
beim Brennen definierte Zeiten und eine geeignete Atmosphäre.
Nichteinhaltung führt zu erhöhten inneren Spannungen,
zu Fehlern am Werkstück oder zu unzureichenden Eigenschaften.
Dünnere Scherben und dicht geformte Werkstücke verhalten
sich günstiger und lassen sich schneller brennen als
großformatige mit größerer Wanddicke.
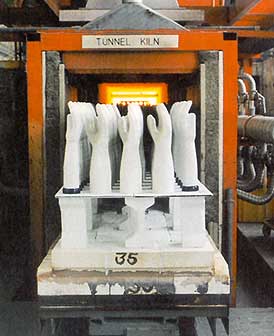
Bild 60: Tunnelofen
Typische Sintertemperaturen:
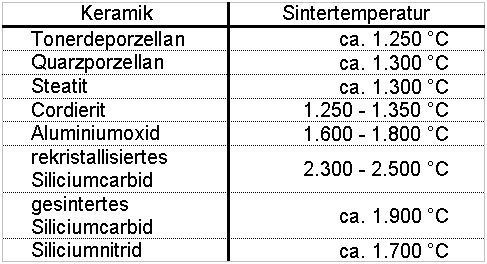
Tabelle 5: Sintertemperaturen keramischer
Werkstoffe
Mit zunehmender Brenntemperatur steigt der Energieeinsatz
für den Sinterprozess überproportional an. Neben
der Energie gehören Brennhilfsmittel aus hochfeuerfestem
Material, mit deren Hilfe das Brenngut gleichmäßig
im Brennraum gestapelt wird, zum besonderen Aufwand.
Bei einigen keramischen Werkstoffen lassen sich durch speziell
unterstützte Sinterverfahren besondere Werkstoffvarianten
erzeugen:
Heißpressen (HP)
dient zur Herstellung von Bauteilen mit annähernd theoretischer
Dichte und ist ein Sintervorgang, der durch einen Pressvorgang
unterstützt wird.
Heißisostatisches Pressen
(HIP)
verleiht vorzugsweise kleinen Bauteilen höchste Dichte
durch Verwendung von isostatischem Gasdruck bis 3.000 bar
bei der jeweiligen Sintertemperatur bis
2.000 °C (z. B. in flexiblen Kieselglashüllen).
|